Introduction
PV system fires are rare but can cause a lot of damage to a building and its contents. While it is rare for panels to catch fire on their own, poor workmanship combined with negligence can cause issues that eventually lead to electrical fires on the roof or at the inverter.
In recent months, GSES has attended multiple sites to conduct investigative fire inspections on commercial solar systems. The findings from the visits concluded that the fire was likely caused by water ingress or loose connections at rooftop isolators. Fortunately, in all instances, major damage was averted due to favourable conditions and the quick responses of personnel onsite and emergency services
As solar fires are a major risk to the reputation of the Australian solar industry as well as an obvious risk to safety and property; it is important to understand the causes of PV system failures and how to prevent them.
Our engineers and inspectors have inspected over 10,000 grid-connected solar PV systems in the past ten years. During this time, we have concluded that there are three main causes of fires:
Cause 1 – Water ingress into DC isolators
DC isolators, especially the DC isolators located at the roof (rooftop isolators), are a known common cause of fires in PV systems. Historically, rooftop isolators have been a requirement in Australia to allow fire safety services and other workers to disconnect the system at the array – i.e. while on the roof. However, with rooftop isolators being more exposed to the elements, they are more prone to damage and deterioration. They are also less visible, resulting in issues occurring at the rooftop isolator often being missed until it is too late. While recent regulatory changes now allow alternatives to rooftop isolators, there will still be millions of rooftop isolators already installed.1
Without proper installation methods to maintain the ingress protection (IP) of the isolator enclosures, water can get in and accumulate inside the isolator enclosure, causing corrosion of the terminals and, in the case of inundated isolators, damage internal components of the isolator too. When the isolator carries current in this state, higher resistance at points where corrosions has occurred, causing a hot joint which can eventually lead to fire.
Figure 2. Evidence of corrosion at an isolator terminal Figure 3 – Partial immersion of the isolator and corrosion evident with watermark and presence of green – copper conductor corroded, and brown – iron screw corroded
Some common points of water entry at DC isolators:
1. Conduit not glued. This allows water to seep in slowly at the connection point, or allow movement which results in the conduit falling out creating a penetration point. Conduit entries, including caps for unused entries, should all be glued.
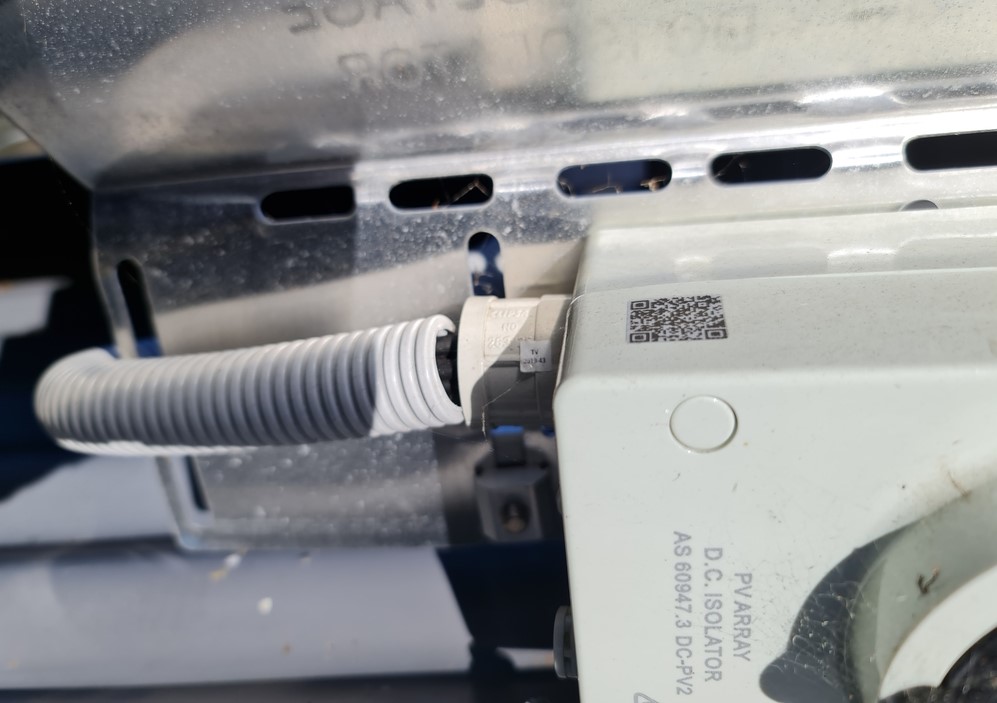
2. Screws not sealed. This can allow water to slowly seep in from the other side of the screw.
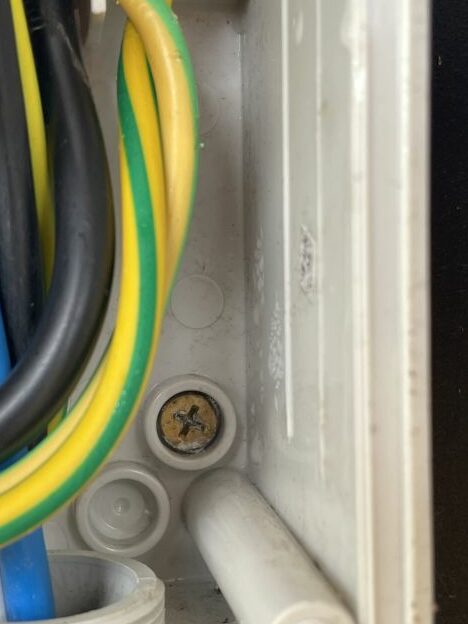
3. Improper cable glands used. Multi-hole cable glands, instead of single hole compression gland, must be used to accommodate the cables entering the conduits. Extra holes that are not used must be plugged up.
4. Improper penetration of enclosures. Drilling holes in an enclosure without sealing them with purpose made products can lead to water seeping in. Penetrations made anywhere other that the lower surface of the enclosure have an increased risk of allowing water to drip onto components or even accumulate in the enclosure.
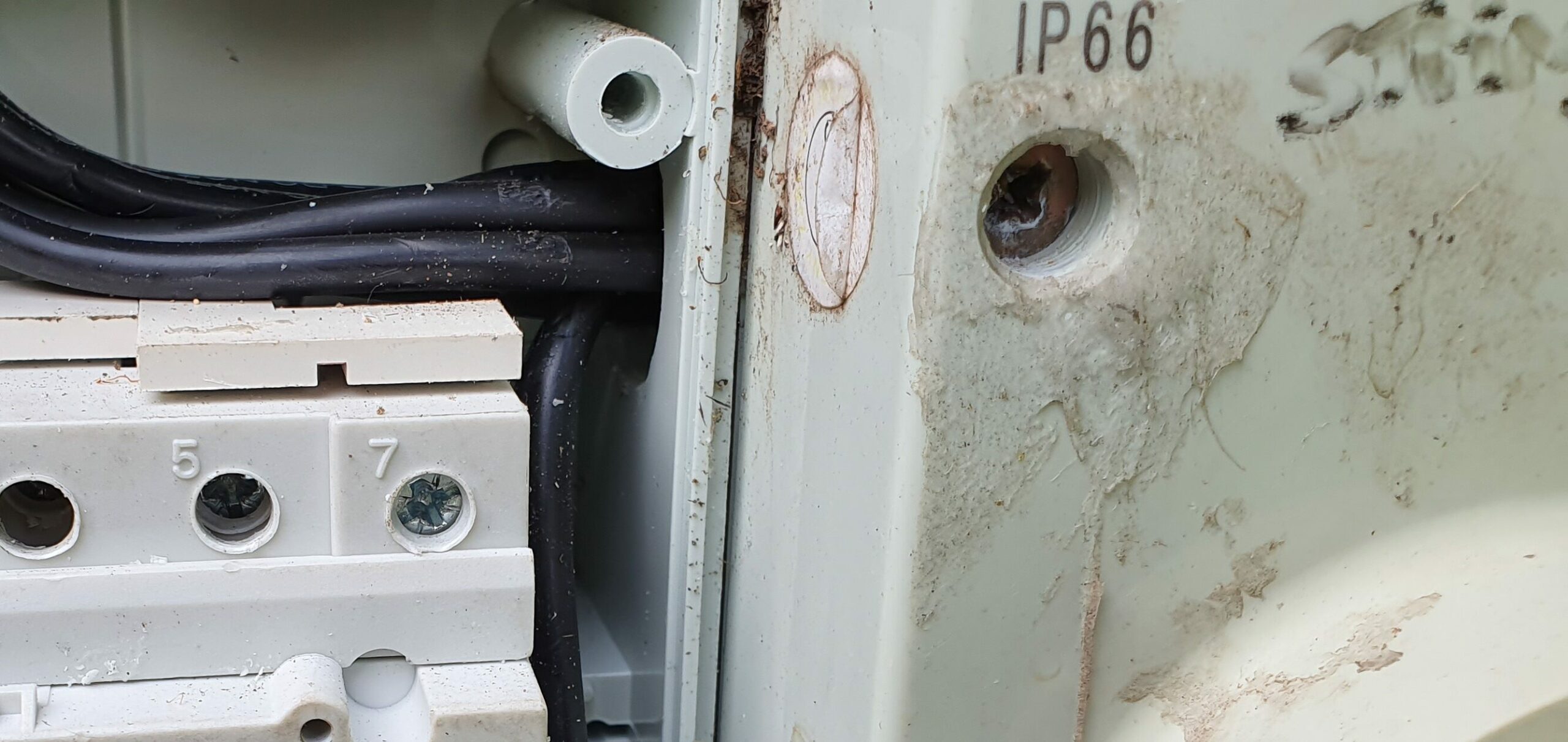
5. Overtightened screws leading to cracked enclosure or loose screws leading to an inadequate seal. Both are cases where the manufacturer’s torque settings have not been followed, allowing water to seep in.
Hopefully, there will be a reduction of instances of water ingress with AS/NZS 5003:2021 removing the requirement for rooftop isolators in specific scenarios. AS/NZS 5003:2021 Clause 4.4.7 outlines installation requirements to prevent water ingress, the above is a subset of the most common non-compliances seen in the field causing water ingress.
Cause 2 – Cable termination
Terminals and other connections need to be properly tightened for the current to flow through properly. When the torque settings are not followed or connections are loose, hot joints can be created. The heat can melt the plastic around the cables and start a fire.
Attention should also be paid to the length and location of the cables in the enclosure to avoid pinching and damaging the cables.
It is important to remember that each plug and socket is also a connection, and loose connectors or joining of connectors of different brand and model can also result in a hot joint on the roof.
Cause 3 – Damage to module
Solar modules are tested to withstand various conditions. However, damage to the module can cause internal cracks that are not easily visible. Microcracks can lead to hotspots in the cell, which then may lead to fires.
Cracks and microcracks in the cell can be caused by:
- Smashed module (golf ball, cricket ball, hail)
- Earthing lugs installed against backsheet causing abrasion
- People walking on modules/improper transport
Another way damage can occur is via delamination of the module backsheet causing water ingress into the panel itself and short-circuit of the module current to earth. This usually does not cause fire; however, it does reduce system output and cause the roof to be hazardous
Prevention
Solar fires are often the result of a number of mistakes and oversights. Most commonly, the risk exists because care has not been taken during installation to keep water out, and fire starts when the issue is not picked up early by the way of monitoring or regular inspections. The severity of fires can be increased if leaf litter is allowed to build up, or common points of failure, e.g. the rooftop isolator, are installed in close proximity to flammable materials.
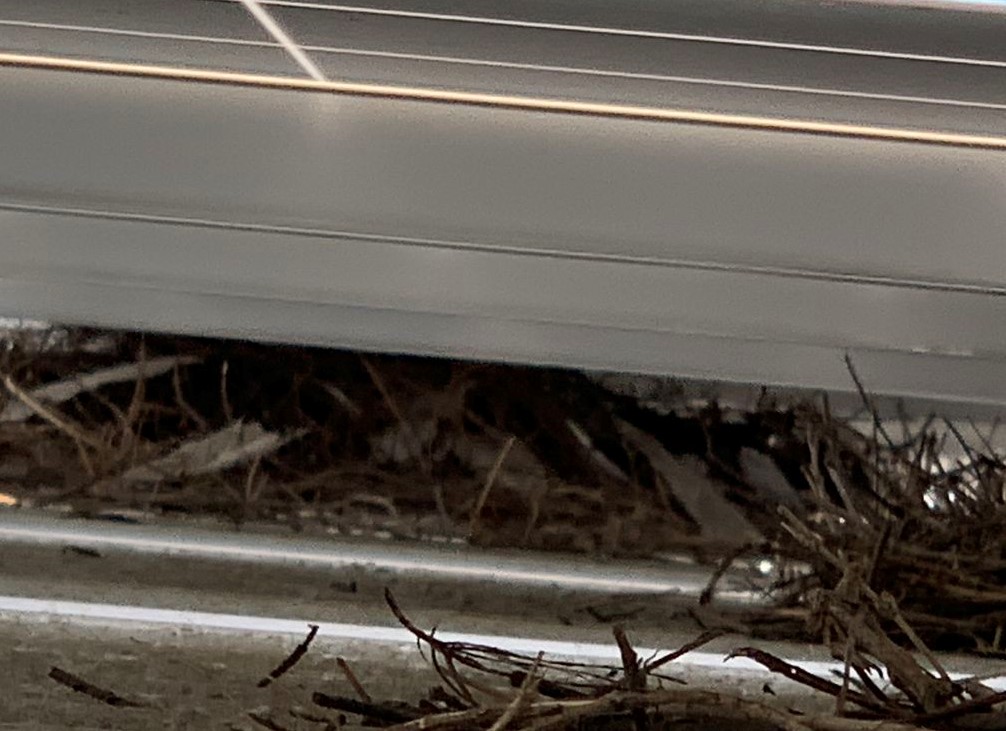
Whether by lack of knowledge or motivation, when the issue isn’t addressed, dangerous situations can occur. But solar fires are avoidable. For big projects, 3rd party independent inspections at the point of handover can help pick up issues right at the start. There should be a plan in place to inspect the system at regular intervals to ensure connections are still tight, ingress protection is maintained and debris at the array is kept to a minimum. Also, make sure to occasionally check the performance of your solar system. This can, in some cases, identify issues before they escalate.
Here are a few things you can do to keep your rooftop PV system operational and safe.
- Use quality products that are less likely to fail and that have reliable warranties.
- Choose reliable installers that are less likely to make installation mistakes. Ensure they have a workmanship warranty.
- Regularly inspect the system. We recommend inspecting the system one year after installation and every 5 years after that. Follow-up inspections could be included in the system procurement contract
- Clean under and around the array. Fire can propagate faster if there are leaves and other debris under the modules.
- Don’t install on combustible material.
- Use asset management tools such as GSES’ ‘Diagno’ to investigate drops in production early. A hot joint or short circuit is likely to reduce the system’s output. Asset management tools will identify if there is an issue with production and prompt the customer or asset manager to inspect the system for faults.
Contact GSES today for more information about how Diagno can help you keep your property safe from the risk of potentially devastating solar fires.
[1] https://www.energy.gov.au/news-media/news/australia-achieves-3-million-rooftop-solar-pv-installations